What defines a particular group of gyroscopic devices, and what are their applications? A specific family of gyroscopes, meticulously designed, possess unique characteristics impacting various fields.
This group of gyroscopic instruments shares a common design principle. Their construction, often involving specialized components and manufacturing techniques, allows for precise control and measurement of rotational motion. These gyroscopes are frequently utilized in navigation systems, aerospace engineering, and specialized industrial machinery. Specific examples include inertial navigation systems and high-precision robotic control. Variations within the family are often categorized by their sensitivity, accuracy, and operating parameters.
The importance of this family of gyroscopic devices stems from their ability to provide extremely precise and stable measurement of angular velocity. Their application within critical systems, like aircraft guidance, ensures reliable performance in demanding situations. The benefits extend to enhanced safety, improved accuracy, and reduced maintenance in high-tech applications. Historical context reveals increasing demands for precision and reliability in these instruments, driving the development of ever-more sophisticated models throughout the years.
Moving forward, the article will explore the diverse applications of gyroscopic technology in detail, including considerations for their performance characteristics and limitations.
Gyro Zepelii Family
Understanding the Gyro Zepelii family necessitates examining its key characteristics and applications. This analysis highlights essential aspects, guiding deeper comprehension of this group of gyroscopic devices.
- Design Principles
- Manufacturing Techniques
- Precision Control
- Angular Velocity Measurement
- Aerospace Applications
- Navigation Systems
- High-Precision Robotics
- Operating Parameters
The Gyro Zepelii family, while encompassing diverse specific models, shares fundamental design principles and manufacturing techniques, resulting in high-precision control. These features enable accurate angular velocity measurements, crucial in aerospace navigation systems and high-precision robotics. Specific applications, such as advanced aircraft guidance systems, rely on instruments capable of maintaining stable orientation despite external forces, highlighting the family's importance in precise measurement and control. Furthermore, the specific operating parameters, sensitivity and accuracy metrics, are tailored for various applications, showcasing the adaptability of this instrument group. Understanding each of these aspects allows for a complete evaluation of their utility in critical technologies.
1. Design Principles
The "Gyro Zepelii family," a classification of gyroscopic devices, is fundamentally defined by its design principles. These principles dictate the construction, components, and operational characteristics, ultimately shaping the device's performance and suitability for various applications. A robust design, including intricate mechanical linkages and precision manufacturing, underpins the family's ability to maintain accurate rotational measurements in complex environments. This meticulous design is paramount for applications such as inertial navigation systems, where small errors can have significant consequences.
Specific design elements within this family include the rotor's material, its construction techniques, and the mechanisms employed for sensing angular momentum changes. The quality of these design choices is directly correlated with the device's precision, stability, and overall reliability. For instance, a gyroscope with a high-strength, lightweight rotor will experience less inertia, enabling faster response times and greater accuracy. Likewise, intricate suspensions minimize external disturbances, ensuring stable operation, which is critical in demanding applications such as aerospace guidance systems. Understanding the design rationale behind the Gyro Zepelii family allows analysts to predict performance parameters and identify potential weaknesses. This understanding is also critical for engineers seeking to adapt or refine these devices for new purposes.
In conclusion, the design principles underpinning the Gyro Zepelii family are not merely technical considerations; they are the cornerstone of functionality and effectiveness. A thorough understanding of these principles, including materials science, mechanical engineering, and sensor technology, enables informed design choices, ultimately optimizing performance and reliability in diverse applications. Challenges remain in optimizing design for specific applications, particularly in extreme environments, but the overall strength of the family hinges on the meticulous execution of its fundamental design principles.
2. Manufacturing Techniques
Manufacturing techniques play a critical role in determining the performance characteristics of the Gyro Zepelii family. Precision in fabrication is paramount, as variations in construction directly impact the gyroscope's accuracy, sensitivity, and stability. Different manufacturing approaches allow for customization to meet varying application needs within this family.
- Material Selection and Processing
The selection and processing of materials are fundamental to achieving the required performance characteristics. Gyroscopes often necessitate specific materials offering a balance of strength, stiffness, low mass, and resistance to environmental factors. Advanced alloys, composites, and specialized coatings are employed to optimize performance. Variations in material properties influence the device's response time, susceptibility to external forces, and overall reliability. For instance, a gyroscope requiring high rotational speeds demands materials with minimal friction characteristics, whereas those operating in harsh environments might necessitate corrosion-resistant coatings. Proper material selection, along with meticulous processing methods, is essential to ensuring the gyroscope operates as designed.
- Precision Machining and Assembly
Accurate machining is crucial for creating the complex geometries and tight tolerances inherent in Gyro Zepelii family devices. Sophisticated machining techniques, including turning, milling, and grinding, are employed to produce components with minimal deviations from the intended design. The assembly process, incorporating precise alignment and bonding procedures, is equally critical to the final performance. Variations in assembly procedures can lead to inconsistencies in the gyroscope's response, impacting its ability to accurately measure angular velocity. Tight tolerances and flawless assembly contribute to the device's ability to maintain stable and accurate performance over extended periods.
- Sensor Integration and Calibration
The integration of sensors and their subsequent calibration are essential components of the manufacturing process. These sensors, often critical to the operation of the devices, must be precisely integrated with the other components for seamless operation. Calibration procedures, which vary depending on the specific type of sensor used, ensure accurate measurements. Variations in sensor integration and calibration accuracy directly affect the overall performance of the gyroscope, and this must be carefully controlled to maintain the required accuracy and reliability within the Gyro Zepelii family.
In summary, the manufacturing techniques employed in producing gyroscopes within the Gyro Zepelii family directly influence their overall performance. Optimized techniques in material selection, precision machining, and meticulous sensor integration collectively contribute to creating highly precise and reliable gyroscopic instruments. Variations in these aspects can lead to substantial discrepancies in the final product's performance characteristics, highlighting the importance of adhering to rigorous standards throughout the manufacturing process. This attention to detail is crucial for maintaining the high level of quality and dependability associated with these advanced instruments.
3. Precision Control
Precision control is inextricably linked to the Gyro Zepelii family. This connection is fundamental, as precise control is the very essence of these instruments. The family's design, encompassing intricate mechanical components and sensitive sensors, prioritizes achieving and maintaining precise rotational control. This precision is crucial for applications requiring consistent orientation and angular velocity measurement, critical in scenarios where even minor errors can have significant consequences. Examples range from guiding spacecraft to navigating advanced robotic systems.
The importance of precision control within the Gyro Zepelii family stems from its impact on accuracy. The instruments' ability to measure and respond to minute changes in angular velocity is paramount. This precision is achieved through meticulous attention to detail during design, manufacturing, and calibration. For instance, in inertial navigation systems used in aircraft, the ability of the Gyro Zepelii family to maintain precise angular measurements ensures consistent and accurate navigation, contributing to flight safety and efficiency. Similarly, precision control is essential in the operation of high-precision robots, enabling them to execute intricate tasks with accuracy and consistency. The practical significance lies in the reliable operation of sophisticated systems where predictable performance is a cornerstone of success.
In conclusion, the inherent need for precision control within the Gyro Zepelii family is undeniable. The instruments' ability to maintain accurate rotational measurements is the bedrock of their effectiveness across a wide range of applications. Understanding this principle underscores the critical role precise control plays in achieving desired outcomes. The ongoing quest for even greater precision within this family continues to drive innovation and refinement in gyroscopic technology, with the potential to lead to further improvements in crucial areas like navigation, aerospace engineering, and robotic automation.
4. Angular Velocity Measurement
Accurate measurement of angular velocity is fundamental to the operation of gyroscopic devices, particularly within the Gyro Zepelii family. The ability to precisely quantify rotational motion is essential for numerous applications, including navigation, aerospace engineering, and advanced robotics. This facet directly impacts the performance and reliability of these systems.
- Precision and Sensitivity
The Gyro Zepelii family prioritizes high precision and sensitivity in measuring angular velocity. This translates to the ability to detect and quantify even minute changes in rotation. Exceptional sensitivity is critical for detecting subtle movements in complex systems, such as aerospace vehicles or precision robotic manipulators. Variations in design and construction within this family influence the instrument's capacity to detect these changes. The range of measurable velocities, from extremely low to relatively high, further defines the capabilities of particular models. This characteristic directly affects the reliability and accuracy of measurements in a given system.
- Stability and Accuracy
Stability in angular velocity measurement is equally important. A gyroscope's ability to maintain a consistent and accurate reading amid external disturbances significantly influences overall performance. The Gyro Zepelii family employs various techniques to enhance stability, including advanced construction methods and sophisticated internal mechanisms. This stability is vital for maintaining consistent orientation in navigation systems or the precise execution of movements in robotics. The level of accuracy in these measurements is inextricably linked to the stability and reliability of the systems they support.
- Real-World Applications
Applications leveraging precise angular velocity measurements within the Gyro Zepelii family are extensive. Inertial navigation systems for aircraft and spacecraft rely heavily on gyroscopes for orientation tracking. These devices enable precise trajectory control, critical for both manned and unmanned flight. High-precision robots also utilize gyroscopes for accurate movement and positioning. Furthermore, the instruments contribute to stabilization in dynamic systems, facilitating applications in scientific research and industrial settings, like advanced drilling rigs.
- Influence on System Design
The accuracy and stability of angular velocity measurement directly influence the design and reliability of broader systems. Navigation systems requiring consistent orientation rely on the precise readings from the Gyro Zepelii family. Likewise, high-precision robots necessitate precise rotation data to execute complex movements. The potential for error within the angular velocity measurement significantly impacts the overall performance of these systems. Engineers and designers carefully consider the limitations of gyroscope technology when developing these complex systems, ensuring that the instrument's specifications meet the system's demands.
In conclusion, angular velocity measurement is a defining characteristic of the Gyro Zepelii family. The precision and stability of these measurements directly affect the functionality and reliability of various systems relying on this technology. Understanding the nuances of measurement techniques and the limitations within this family of gyroscopes is essential for engineers and analysts to accurately design and implement systems requiring precise angular data.
5. Aerospace Applications
The Gyro Zepelii family plays a critical role in contemporary aerospace applications. Sophisticated gyroscopic instruments within this family are indispensable components in inertial navigation systems, enabling precise orientation and trajectory control for a broad spectrum of aircraft. The accuracy of angular velocity measurements directly impacts the performance and safety of flight operations. Without reliable gyroscopic data, critical functions like aircraft stabilization, navigation, and guidance become significantly compromised.
Real-world examples abound. Modern commercial airliners and military aircraft rely heavily on inertial navigation systems incorporating these advanced gyroscopes. Precise orientation information, derived from consistently accurate angular velocity measurements, enables pilots to maintain stable flight paths, especially during periods of poor visibility or in challenging atmospheric conditions. Similarly, in spacecraft navigation and trajectory correction, the Gyro Zepelii family plays a crucial part. The ability of these instruments to provide precise and stable angular velocity readings is essential in complex space missions, enabling spacecraft to execute precise maneuvers and maintain accurate trajectories. The high degree of precision required in these applications necessitates the use of advanced instruments within the Gyro Zepelii family.
The significance of this connection extends beyond practical application. Understanding the intricacies of aerospace applications underscores the criticality of precision in gyroscopic technology. High-performance gyroscopes, exemplified by the Gyro Zepelii family, are vital for ensuring accurate navigation and control in demanding aerospace environments. Challenges remain in maintaining performance in extreme temperature fluctuations and high-vibration environments, but ongoing research continues to address these issues, refining instrument design and fabrication techniques for future aerospace applications. This underscores the vital role of meticulous engineering in the development and implementation of gyroscopic technologies that meet stringent aerospace standards.
6. Navigation Systems
Navigation systems, particularly those demanding high accuracy and reliability, heavily rely on the precision of gyroscopic instruments. The Gyro Zepelii family, with its advanced design and manufacturing techniques, stands as a crucial component within these systems. The integration of these gyroscopes is pivotal in establishing a stable and accurate frame of reference, enabling precise positioning and guidance in diverse environments. Understanding this connection reveals the vital role gyros play in the functionality and effectiveness of modern navigation systems.
- Intrinsic Orientation and Stability
Gyro Zepelii family devices provide inherent orientation and stability in navigation systems. Their capacity to measure and maintain rotational axes, regardless of external disturbances, is a cornerstone of accurate navigation. These instruments function as internal compasses, ensuring a stable reference frame. In aircraft or spacecraft navigating complex trajectories, accurate readings of the vehicle's orientation, even during sudden maneuvers or atmospheric turbulence, are indispensable for accurate positioning and guidance.
- Inertial Measurement Units (IMUs)
Gyroscopes within the Gyro Zepelii family are often integral to IMUs. These units combine gyroscopic data with accelerometers to provide a complete picture of a vehicle's motion in three dimensions. This integrated data is crucial for generating accurate navigational information for long-distance travel or complex flight maneuvers, allowing for continuous updates in a vehicle's location without external references like GPS signals.
- Autonomous Navigation Systems
Gyro Zepelii-based IMUs are vital for autonomous navigation systems. These systems, found in various applications from drones to self-driving vehicles, rely on the consistent and precise angular velocity readings to guide robots along intended trajectories. The continuous assessment of the robot's orientation, facilitated by the gyroscopic sensors, is essential for autonomous decision-making and smooth navigation.
- Precision in Diverse Environments
The effectiveness of the Gyro Zepelii family in navigation extends beyond typical applications. Their advanced design often includes features mitigating external factors, such as temperature fluctuations and vibrations. This resilience allows these gyroscopes to maintain accuracy in diverse environmentsfrom extreme altitudes in aerospace applications to rugged terrain in robotics and surveying. The stable performance in various conditions makes the Gyro Zepelii family a dependable component in a wide range of navigation systems.
In conclusion, the Gyro Zepelii family's precise angular velocity measurements are fundamental in modern navigation systems. The intricate interplay between gyroscopic stability, IMU integration, autonomous navigation capabilities, and resilience in diverse environments highlights the crucial role these instruments play in ensuring reliable, accurate, and efficient navigation across various platforms and applications. The precision and dependability of the Gyro Zepelii family directly contribute to the advancement and application of high-precision navigation technologies.
7. High-Precision Robotics
High-precision robotics rely heavily on precise control mechanisms. Gyroscopic instruments, particularly those within the Gyro Zepelii family, are integral to achieving this precision, providing crucial data for accurate movement and orientation. The tight tolerances and demanding requirements of these robotic applications necessitate the use of highly sensitive and stable gyroscopic technology.
- Accurate Movement and Orientation
Precise movements are paramount in high-precision robotics. Gyroscopes within the Gyro Zepelii family, with their high degree of accuracy in measuring angular velocity, contribute significantly to this precision. The instruments consistently provide accurate orientation data, which is critical for complex tasks such as assembly, micro-surgery, and intricate manufacturing processes. The ability to detect and react to minute changes in orientation and rotation is fundamental in enabling machines to perform delicate operations and maintain precise positioning.
- Stable Platform and Enhanced Stability
Maintaining a stable platform for high-precision robotic operations is crucial. The Gyro Zepelii family enables the construction of stable platforms, mitigating the effects of external disturbances. This enhanced stability allows for consistently accurate movements, regardless of external factors such as vibrations or tremors. Without the stability provided by these gyroscopes, the precision required for tasks such as micro-machining or complex assembly procedures would be significantly compromised.
- Real-time Feedback and Control Systems
Gyro Zepelii family gyroscopes are often embedded within real-time feedback and control systems in high-precision robotics. The gyroscopic data allows for continuous monitoring and adjustment of movement, ensuring consistent accuracy throughout the operation. This real-time feedback loop allows for dynamic responses to unexpected changes in the environment or the task itself, critical for maintaining precision and avoiding errors during intricate processes like laser cutting or material deposition.
- Complex Task Execution
The precise and stable orientation provided by Gyro Zepelii family gyroscopes is essential for complex robotic tasks. Tasks demanding intricate movements, precise positioning, and rapid adaptations to changing conditions benefit significantly from this technology. Examples include highly automated assembly lines for advanced electronics, intricate surgical procedures with robotic assistance, and advanced machining applications.
In summary, the Gyro Zepelii family's precise angular velocity measurements, combined with their stability, facilitate crucial functions within high-precision robotics. The instruments enable reliable movement control, accurate orientation, and efficient execution of complex tasks. The integration of these gyroscopic technologies is critical for maintaining the required precision and responsiveness in these advanced robotic systems.
8. Operating Parameters
Operating parameters are crucial factors defining the performance and utility of gyroscopic instruments, particularly within the Gyro Zepelii family. These parameters encompass a range of characteristics, influencing how effectively the devices function in various applications. Understanding these parameters is essential for selecting the appropriate gyroscope for a specific application and ensuring optimal performance.
- Operating Temperature Range
The operating temperature range directly impacts the accuracy and stability of gyroscopic measurements. Variations in temperature affect material properties, leading to changes in the instrument's response and potentially compromising accuracy. Gyroscopes designed for high-performance applications often have stringent temperature ranges to maintain consistent performance. For example, gyroscopes employed in aircraft operating at high altitudes require a wider operating temperature range compared to those in laboratory environments. The selection of a gyroscope must consider the anticipated temperature fluctuations to ensure reliable performance.
- Angular Velocity Measurement Range
The angular velocity measurement range specifies the range of rotational speeds a gyroscope can accurately measure. Certain applications require gyroscopes that can detect very low rotational speeds, while others need instruments capable of handling high-speed rotations. The Gyro Zepelii family may encompass models with distinct velocity ranges, catering to diverse needs in navigation or robotic control. For instance, a gyroscope designed for an autonomous vehicle would require a wider measurement range than one intended for precision laboratory equipment. The appropriate range selection directly affects the gyroscope's utility in a specific application.
- Sensitivity and Resolution
The sensitivity and resolution of a gyroscope describe its ability to detect small changes in rotational velocity. Higher sensitivity and resolution are typically required for applications demanding precise orientation and movement control. Within the Gyro Zepelii family, models are often categorized by their sensitivity, with some designed for extremely precise measurements. Applications requiring very fine control, like micro-robotics, necessitate high-sensitivity gyroscopes. Conversely, systems with less stringent precision requirements might use gyroscopes with lower sensitivity.
- Environmental Factors (Vibration and Shock Resistance)
Environmental factors, including vibration and shock resistance, are critical in many applications. Gyroscopes designed for aerospace or robotic applications need to withstand substantial vibrations and shocks. Components within the Gyro Zepelii family vary in their resilience to these factors, with some designed to operate reliably in high-stress environments. This robustness is crucial for ensuring accurate readings amidst external disturbances. A gyroscope's ability to withstand these forces significantly impacts its utility in challenging operating conditions.
In conclusion, operating parameters are essential considerations when selecting and utilizing gyroscopes within the Gyro Zepelii family. The interplay of factors like temperature, velocity range, sensitivity, and environmental resistance directly impacts a gyroscope's effectiveness. Careful consideration of these parameters ensures appropriate selection and optimal performance in diverse applications, contributing to the accurate and reliable operation of complex systems involving precise orientation and control.
Frequently Asked Questions
This section addresses common inquiries regarding the Gyro Zepelii family of gyroscopic instruments. These questions and answers aim to provide clear and concise information about the key characteristics, applications, and considerations related to this technology.
Question 1: What are the defining characteristics of the Gyro Zepelii family?
The Gyro Zepelii family is distinguished by its high precision in angular velocity measurement. This precision is achieved through meticulous design principles and manufacturing techniques. The specific construction, utilizing advanced materials and sophisticated assembly processes, ensures consistent performance and minimizes errors. Key features often include a high degree of stability, resilience to external factors like vibration, and a broad operational temperature range.
Question 2: What are the primary applications of Gyro Zepelii family gyroscopes?
Gyro Zepelii family gyroscopes are integral components in numerous applications demanding high-precision orientation and motion control. These include inertial navigation systems for aircraft and spacecraft, high-precision robotics, and advanced sensor systems. Their accuracy and reliability are critical in applications requiring sustained orientation and stable platform function.
Question 3: How does the Gyro Zepelii family compare to other gyroscopic technologies?
Compared to other gyroscopic technologies, the Gyro Zepelii family typically exhibits higher sensitivity, accuracy, and stability. Specific design choices and manufacturing processes yield superior performance in demanding applications, making them suitable for situations where high precision is paramount. However, specific applications and operational requirements should inform the choice of a particular gyroscope model.
Question 4: What are the limitations of Gyro Zepelii family devices?
While generally highly reliable, Gyro Zepelii family instruments are not without limitations. These include cost, size, and weight, which may restrict their use in certain applications. Additionally, the instruments' sensitivity to external disturbances and the need for calibration should be considered. Careful assessment of these limitations is critical when designing systems integrating these gyroscopes.
Question 5: What factors should be considered when selecting a gyroscope from the Gyro Zepelii family?
Selecting the appropriate gyroscope from the Gyro Zepelii family necessitates careful consideration of factors such as the desired operating temperature range, required angular velocity measurement range, sensitivity, and resilience to environmental factors like vibration and shock. System integration requirements and expected performance need to be evaluated to ensure compatibility and optimal results.
Understanding these frequently asked questions provides a comprehensive overview of the characteristics and applications of the Gyro Zepelii family. These devices are integral in modern technologies demanding precise measurement and control.
Moving forward, the article will explore advancements and future trends in gyroscopic technology.
Conclusion
The Gyro Zepelii family embodies a crucial advancement in gyroscopic technology. This analysis has underscored the family's defining characteristics, encompassing meticulous design principles, sophisticated manufacturing techniques, and exceptional performance capabilities. Key aspects explored include the instruments' role in precise angular velocity measurement, their application in inertial navigation systems, high-precision robotics, and their critical function in diverse aerospace applications. The exploration further highlighted the importance of operating parameters, such as temperature range, velocity measurement capacity, and environmental resilience. This study demonstrates the indispensable nature of Gyro Zepelii instruments in systems demanding accurate orientation and motion control.
The future of precision engineering is intrinsically linked to the advancement and refinement of gyroscopic technology. Continued research and development within the Gyro Zepelii family are pivotal for further enhancing the instruments' performance capabilities, expanding their operational range, and addressing emerging challenges in dynamic environments. This, in turn, will contribute to the advancement of critical systems across various sectors, including aerospace, robotics, and navigation. The unwavering pursuit of higher precision and stability in these instruments represents a fundamental step toward even more sophisticated and reliable technological advancements in the future.
Article Recommendations
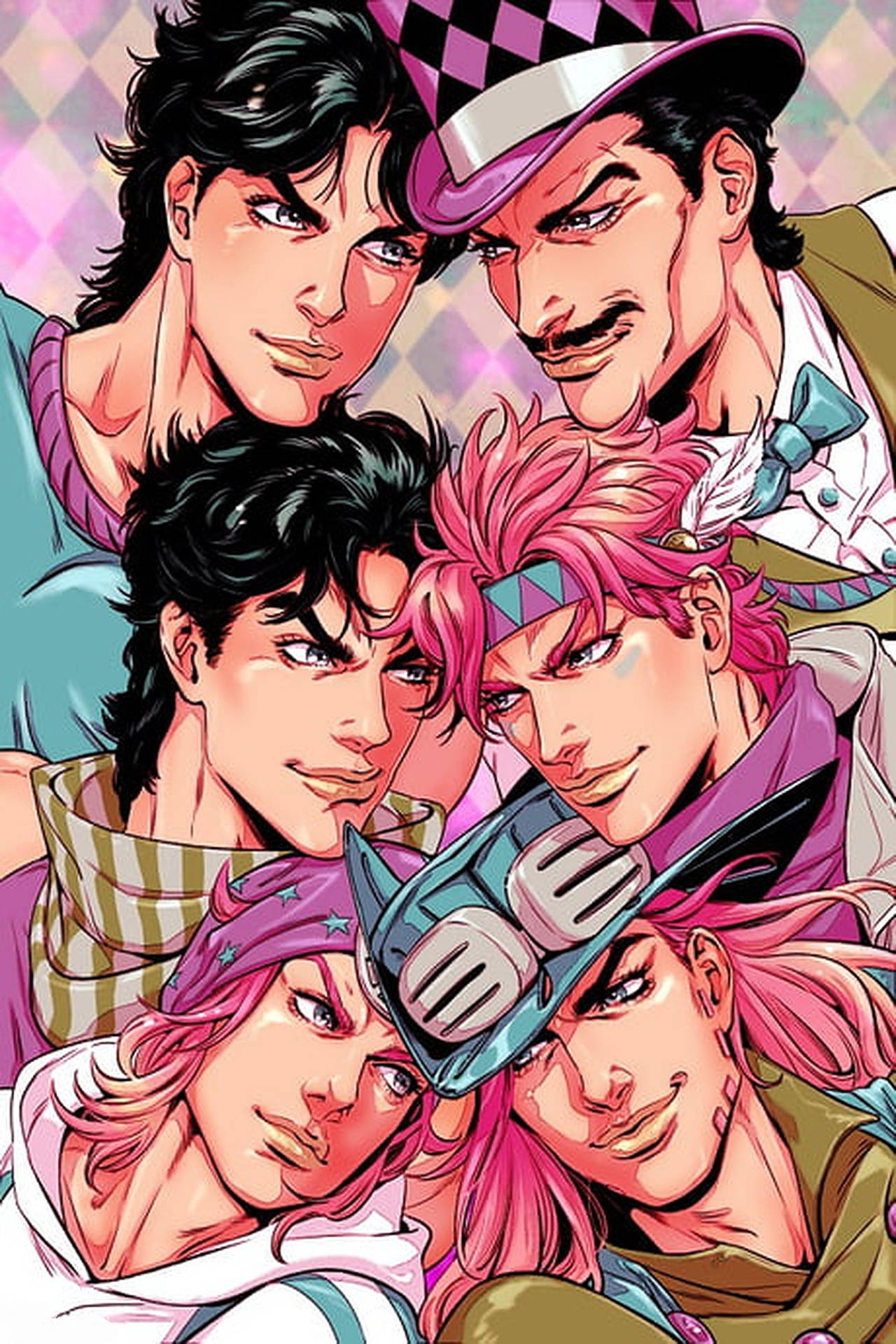
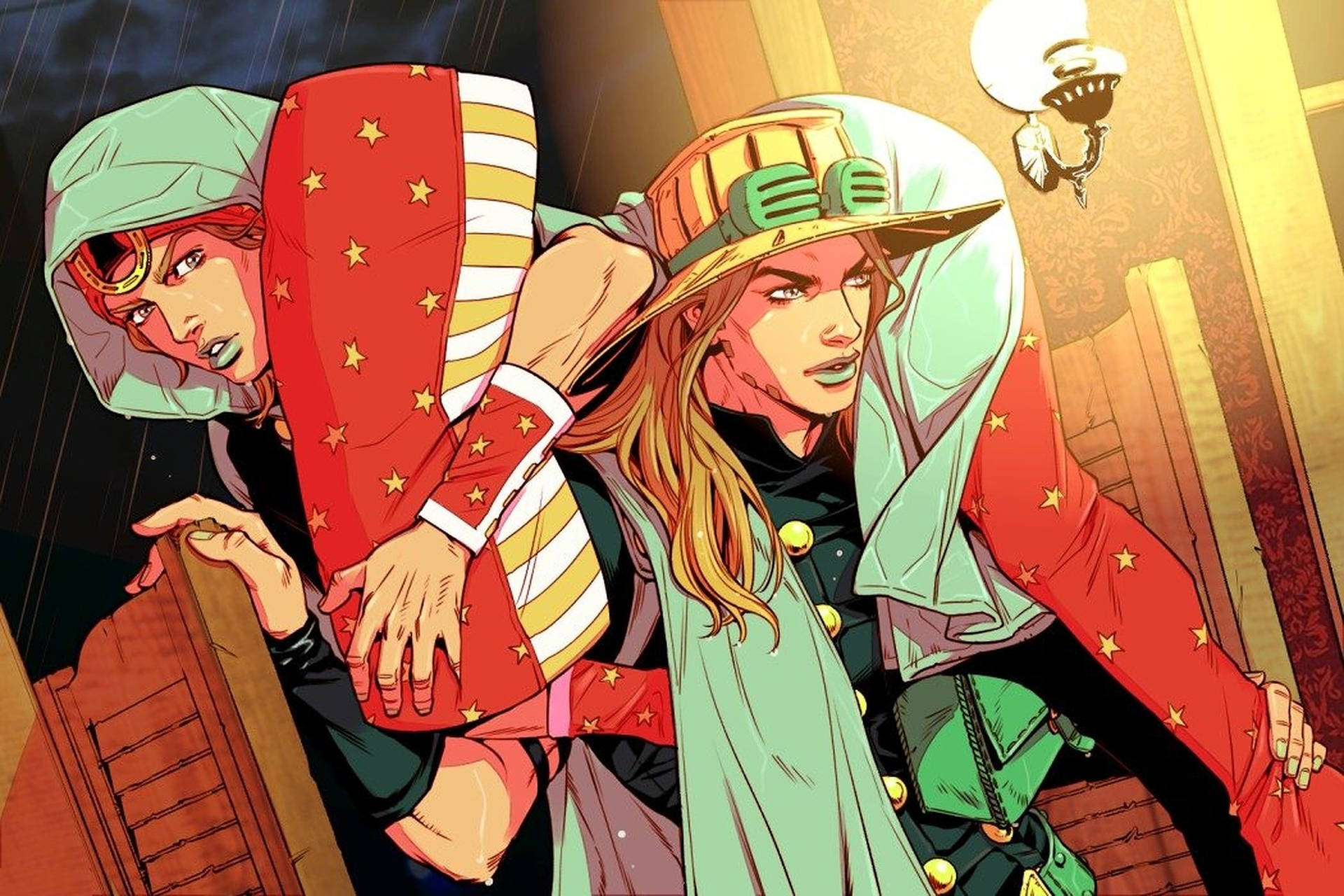
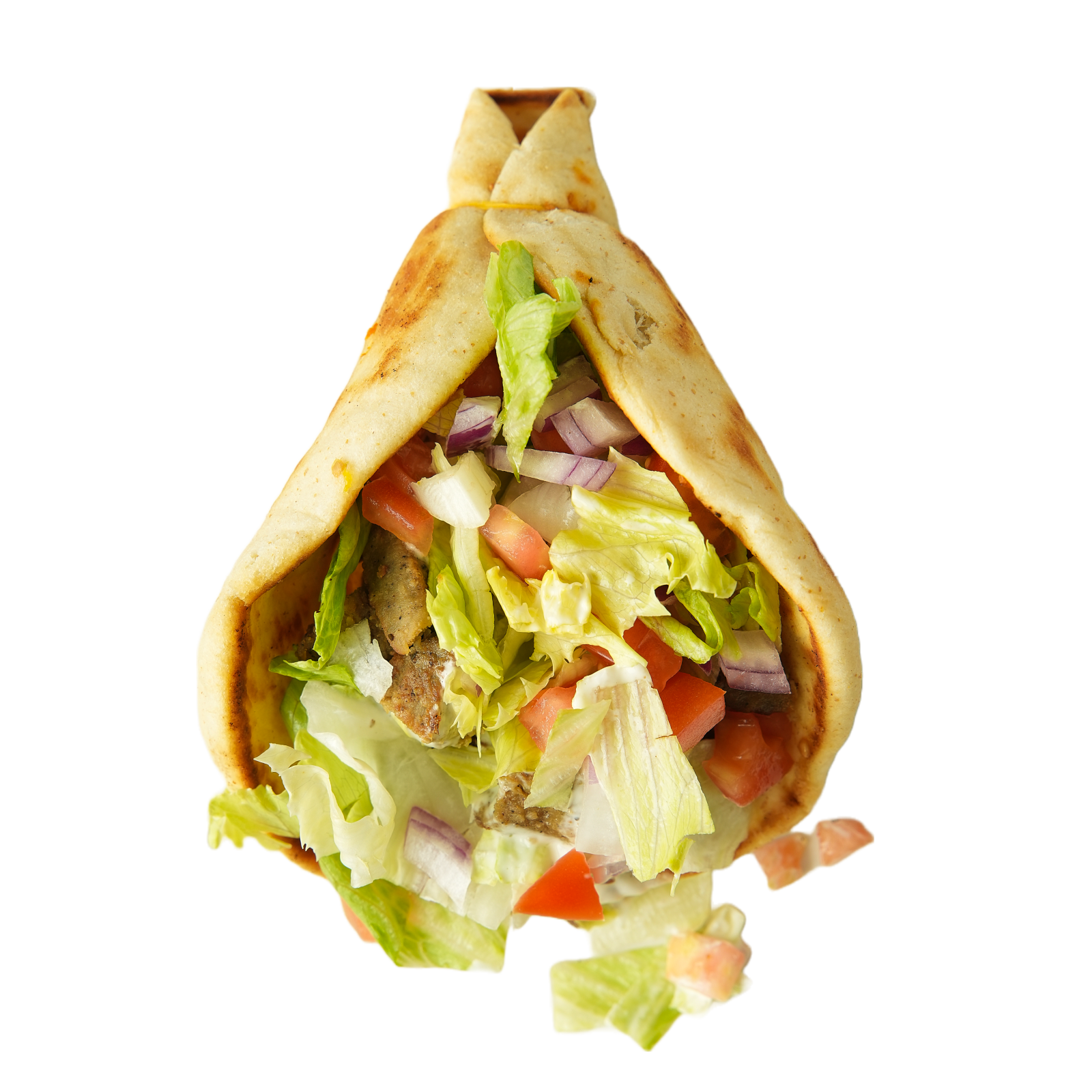
ncG1vNJzZmibkafBprjMmqmknaSeu6h6zqueaJulocG2vsClZJuZoqe2pr7SaJ6yqp9ix6a8xKWgomWWlrqquNhnn62lnA%3D%3D