What are the advantages of these specialized facilities, and how do they impact industry?
These facilities, often located near raw material sources or major transportation hubs, are specifically designed for processing and refining various materials. Examples include processing grains into flour, or crushing and separating ores. They can also encompass sophisticated manufacturing steps, involving complex machinery and techniques for transforming raw inputs into finished products.
The importance of these facilities hinges on their role in efficient production and distribution. Their strategic locations enable cost-effective access to necessary resources, minimizing transportation expenses. Optimized processing often reduces waste and increases yield, translating to higher profitability for businesses. Historically, advances in technology and engineering have significantly improved the efficiency and capacity of these processing operations, leading to broader economic impact. Modern examples can be found across many industries, from agriculture to mining, contributing substantially to global supply chains.
Let's now delve deeper into the specific applications and benefits of these facilities across various sectors. We will investigate the impact of technological advancements and explore emerging trends in these facilities.
Farad Mills
Understanding the operational and structural aspects of these processing facilities is essential for comprehending their role in modern industry.
- Processing
- Materials
- Efficiency
- Capacity
- Technology
- Location
These aspects are interconnected. Processing specific materials efficiently requires consideration of capacity and technology. Optimal location minimizes transportation costs, further enhancing efficiency. Advances in technology directly influence processing capacity, impacting overall output. Examples include grain mills, mineral processing plants, and various manufacturing facilities, each with its unique processing needs and structural demands.
1. Processing
Processing, a fundamental aspect of industrial activity, plays a critical role in transforming raw materials into usable products. This transformation is central to the function of facilities like mills, where raw materials undergo various stages of refinement. Understanding the nature of processing is crucial for assessing the overall efficiency and effectiveness of these operations.
- Raw Material Transformation
Processing involves the systematic alteration of raw materials to achieve a desired state. This can encompass various stages, including extraction, refinement, and combination. In mills, for example, grains are processed into flour, a more readily consumable form. This transformation is crucial for increasing the utility and value of the initial materials.
- Efficiency and Yield
Efficient processing maximizes the output from raw materials, minimizing waste. Optimizing processes in mills, whether grain or ore, directly affects overall profitability. Techniques aimed at minimizing losses during processing are paramount in creating a more sustainable and economically viable operation.
- Technological Advancement
Processing techniques have evolved alongside technological advancements. Modern mills often leverage automation and advanced machinery to expedite processing and improve consistency in product quality. These innovations contribute to heightened production volume and more refined outputs.
- Quality Control
Maintaining consistent product quality is crucial in processing. Quality control measures are inherent in the operation of mills. Maintaining established standards throughout the various processing stages ensures a consistent and high-quality product, which is often a prerequisite for market acceptance.
In summary, processing is fundamental to the operation of facilities like mills. The various facets of processing, from the initial transformation of raw materials to quality control measures, directly impact the efficiency, profitability, and overall effectiveness of these facilities.
2. Materials
The nature of materials processed within these facilities is fundamental to their operation. The selection, characteristics, and properties of materials directly influence the design, efficiency, and profitability of processing operations. This section explores key considerations related to materials within the context of these processing centers.
- Raw Material Sourcing and Availability
The accessibility and cost of raw materials are critical factors. Facilities strategically located near resources benefit from lower transportation costs and greater reliability of supply. Fluctuations in raw material prices directly affect operational expenses and profitability. For example, a grain mill situated far from agricultural zones might face higher costs and potential supply disruptions, impacting production.
- Material Properties and Processing Requirements
Specific material properties, such as hardness, density, and chemical composition, dictate the processing methods employed. Different materials demand different equipment and techniques. A mineral processing facility, for instance, requires equipment tailored to the particular ores being processed. The characteristics of the material directly influence the design and capacity of the facility itself.
- Material Handling and Storage
Efficient handling and storage of materials are critical to overall operational efficiency. Effective systems for receiving, sorting, and storing materials minimize downtime and reduce waste. This is particularly vital in facilities handling large volumes of materials, where optimization of these processes becomes crucial. For example, a facility handling coal must implement secure and efficient storage solutions for stockpile management.
- Waste Management and By-products
The processing of certain materials generates by-products or waste. The management of these materials is essential for both environmental sustainability and economic viability. Optimizing waste disposal practices and exploring the potential value of by-products is crucial for these types of facilities. This can involve recycling, repurposing, or disposing of waste materials responsibly. For instance, wood processing facilities may create sawdust that can be used as a fuel source, or in some other applications.
Ultimately, the proper selection and management of materials are critical considerations for the optimal operation and success of these processing facilities. The efficiency, sustainability, and profitability of such facilities are fundamentally tied to the effective handling and processing of the materials involved.
3. Efficiency
Efficiency in processing facilities is paramount. Optimizing operations minimizes waste, reduces costs, and maximizes output. In facilities handling large volumes of materialwhether grain, minerals, or other raw substancesefficiency translates directly into increased profitability and reduced environmental impact. The interplay between design, technology, and operational procedures is key to achieving this efficiency. Efficient use of space, equipment, and labor is crucial. Examples range from optimized layout of processing machinery in a flour mill to streamlined logistics in a mineral processing plant. The consequence of poor efficiency includes elevated operating expenses, lower yields, and greater environmental burden.
Several factors contribute to efficiency in processing facilities. Streamlined workflows, advanced machinery, and precise control systems are critical components. Modern facilities increasingly utilize automation and data analytics to optimize processes. Real-time monitoring and predictive maintenance can prevent costly breakdowns and ensure consistent operation. For instance, a grain mill equipped with advanced sorting technology can effectively separate grains of varying qualities, leading to improved product consistency and reduced waste. Similarly, a mineral processing plant using advanced crushing and screening equipment can maximize the extraction of valuable minerals, minimizing tailings and environmental impact. Efficient material handling systems, optimized storage capacity, and well-trained personnel all contribute to overall operational efficiency. The efficiency gains are not just financial; they are also a significant contributor to sustainability.
In conclusion, efficiency is not simply a desirable quality; it's fundamental to the effective and sustainable operation of processing facilities. Optimizing processes, adopting advanced technologies, and focusing on streamlined workflows are crucial steps in achieving this efficiency. Understanding and continuously improving efficiency not only enhances profitability but also reduces the environmental footprint of these operations, highlighting a critical connection between economic viability and ecological responsibility.
4. Capacity
Capacity, in the context of processing facilities, dictates the maximum volume of material that can be processed within a specific timeframe. This crucial factor directly impacts the operational efficiency and output of "farad mills" or similar processing centers, influencing their profitability and scalability. The design and operational aspects of a processing facility must align with its intended capacity for optimal performance. Understanding various facets of capacity is thus essential for evaluating the effectiveness and long-term viability of such facilities.
- Design and Infrastructure
The physical design of the facility significantly influences its capacity. The layout of processing equipment, the size of storage areas, and the infrastructure supporting material flow all contribute to the overall capacity. A large grain mill designed with ample storage space and efficient conveyor systems will have a higher capacity than one with restricted space and rudimentary handling systems. Facilities must be appropriately designed to handle the volume and type of material anticipated.
- Technological Integration
Technological advancements play a crucial role in increasing capacity. Automation, advanced machinery, and optimized processing techniques allow facilities to handle more material in less time. Modern equipment and control systems enable greater throughput and yield while simultaneously enhancing operational efficiency. In mining operations, sophisticated crushing and screening technologies increase ore processing capacity.
- Operational Procedures
Efficient operational procedures are essential for maximizing the utilization of existing capacity. Optimizing workflows, minimizing downtime, and ensuring proper staffing levels directly affect the facility's capacity to process material. A well-managed and coordinated workforce is critical to operating at full capacity, preventing bottlenecks or inefficiencies in processing stages. Streamlining the flow of raw materials through the facility is fundamental to optimal utilization of capacity.
- Scalability and Future Needs
Capacity planning should anticipate future growth and demand. Facilities must have the potential for expansion or modification to accommodate increasing volumes of material in the future. Modular designs and flexible layouts can enhance scalability and make a facility adaptable to changing production demands. A processing plant with a modular design can more easily adapt to fluctuations in demand and evolving market needs.
Ultimately, capacity in processing facilities is a multifaceted issue encompassing design, technology, operations, and future projections. Balancing these factors is critical to creating efficient and economically viable operations. By effectively planning and managing capacity, "farad mills" or similar facilities can maximize profitability, sustainability, and long-term viability. This understanding is equally vital in determining the suitability of a processing facility to meet the expected demand and ensure its operational success in the relevant industry.
5. Technology
Technological advancements are inextricably linked to the performance and efficiency of processing facilities like "farad mills". Modern innovations have dramatically reshaped these operations, enhancing productivity, minimizing waste, and improving overall output. The application of advanced technologies is crucial for maintaining competitiveness and adaptability in the face of evolving industrial demands.
- Automation and Robotics
Automation has become integral to many processing facilities. Robotic systems can handle repetitive tasks such as material handling, sorting, and packaging, drastically reducing labor costs and improving processing speed. Sophisticated robotic arms are used in various applications, from the precise sorting of grains in mills to the automated assembly of complex manufactured components.
- Advanced Sensing and Control Systems
Sensors and sophisticated control systems monitor various parameters within the processing facility in real time. These systems enable precise control of environmental conditions, material flow, and equipment performance. Data collected from sensors can be used to optimize processes, identify potential issues before they escalate, and implement corrective measures, thereby maximizing output and minimizing downtime. This applies across industries, from monitoring temperature and humidity in food processing to detecting anomalies in the composition of raw materials in a refinery.
- Data Analytics and Machine Learning
Data generated by sensors and other systems can be analyzed to identify patterns and trends. Machine learning algorithms can be employed to predict equipment failures, optimize processing parameters, and predict future demands. This data-driven approach allows for proactive maintenance, minimizing downtime and optimizing resource utilization. Examples include using machine learning to predict optimal blending ratios in chemical plants or to forecast grain yield based on historical data and weather patterns.
- 3D Modeling and Simulation
3D modeling and simulation tools are used to design and optimize processing layouts, equipment placement, and material flow pathways. Simulating processes before implementation allows for identification of potential bottlenecks, inefficiencies, and safety concerns. This approach significantly reduces the risk of costly errors and improves the overall efficiency of the facility, whether designing a grain silo or a complex chemical reactor.
These technological advancements, from automation to sophisticated data analysis, are transforming processing facilities. By integrating these technologies, "farad mills" and similar operations can achieve unprecedented levels of efficiency, reduce operational costs, minimize environmental impact, and adapt to evolving market demands. The ongoing evolution of technology will likely continue to shape the future of these facilities, driving greater productivity and innovation across various industries.
6. Location
Location is a critical determinant of the success and efficiency of processing facilities. The strategic positioning of a facility significantly impacts its cost structure, accessibility to raw materials, and market reach. Proximity to raw materials minimizes transportation costs, reduces processing time, and diminishes environmental impact from long-distance transport. Conversely, proximity to markets facilitates quick delivery, reduces warehousing needs, and allows for more rapid response to shifts in demand. An ideal location balances these competing interests, acknowledging the interplay of logistics and economic factors.
Consider a grain mill. A location near agricultural fields reduces the cost of transporting raw materials, leading to lower operating expenses. Similarly, a mill situated near major urban centers gains access to a larger consumer base, potentially increasing market share. Alternatively, a mineral processing plant strategically placed near mining operations benefits from cost-effective access to raw ores. The location directly affects processing time and, consequently, the facility's throughput. Conversely, a plant situated far from both raw materials and markets faces increased transportation costs, potentially diminishing profitability. Real-world examples abound, showcasing the direct correlation between location and the viability of a processing facility.
Understanding the importance of location in the context of processing facilities is essential. Strategic location decisions involve a complex interplay of logistical and economic factors. Balancing the need for proximity to raw materials, markets, and transportation infrastructure is crucial. Analyzing existing infrastructure, potential expansion capabilities, and local regulations is critical. A thorough understanding of location-based factors enables informed decision-making during the planning and implementation phases of facility development. This knowledge is also important in assessing the competitiveness of existing facilities and predicting their future success in a dynamic market environment.
Frequently Asked Questions about Processing Facilities
This section addresses common inquiries regarding processing facilities, focusing on key aspects of their operation and function. Understanding these points clarifies the role and impact of these facilities in various sectors.
Question 1: What are the primary functions of processing facilities?
Processing facilities, often called mills or processing plants, serve to transform raw materials into usable products or components. This transformation can involve various stages, including refining, extraction, or combining materials. Efficient processing increases the value and utility of raw materials, impacting diverse industries, from agriculture and mining to manufacturing and energy production.
Question 2: What factors influence the efficiency of these facilities?
Several factors influence efficiency. Strategic location in relation to raw materials and markets significantly reduces transportation costs and processing time. Modern technology, including automation and advanced machinery, optimizes processes, reduces waste, and increases throughput. Efficient operational procedures, effective management, and well-trained personnel further enhance processing capacity and minimize downtime.
Question 3: How do technological advancements impact processing facilities?
Technological advancements are fundamental to operational improvements. Automation reduces labor costs and improves processing speed. Sensors and control systems facilitate real-time monitoring and precise control, minimizing waste and optimizing procedures. Data analytics and machine learning provide predictive capabilities for proactive maintenance and process optimization.
Question 4: What considerations are involved in choosing a location for a processing facility?
Strategic location decisions are paramount. Proximity to raw materials minimizes transportation costs. Access to markets allows for efficient product distribution. Consideration of existing infrastructure, including transportation networks, and regulatory frameworks in the target area is critical. Balancing these factors is key for successful facility operation.
Question 5: How do processing facilities contribute to sustainability?
Efficient processing minimizes waste and optimizes resource utilization, contributing to sustainability. Advanced technologies and efficient operational procedures can reduce energy consumption. Sustainable practices, including waste management and by-product utilization, lessen the environmental impact of these operations. These facilities can contribute to responsible resource management within their specific industrial sectors.
In conclusion, processing facilities play a critical role in modern industry by effectively transforming raw materials into valuable products. Understanding their functions, operating principles, and the influence of various factors is crucial for evaluating their impact across different industries.
Let's now explore specific applications and case studies of processing facilities in various sectors.
Conclusion
This exploration of processing facilities, often exemplified by "farad mills," reveals their multifaceted significance within modern industry. The efficient processing of raw materials is a fundamental aspect, impacting diverse sectors from agriculture to manufacturing. Key considerations include strategic location for resource proximity, the application of advanced technology for increased capacity and efficiency, and the careful management of materials to minimize waste. The operational success and sustainability of these facilities hinge on the interplay of these factors. Understanding these interdependencies provides insight into the economic and environmental impact of these processing hubs. Ultimately, the success of these operations hinges on a deep understanding of materials, processes, technology, and market demands.
Moving forward, continued innovation in technology and operational practices will be crucial for the continued success and sustainability of processing facilities. The industry must adapt to evolving market demands, increasingly stringent environmental regulations, and the need for more responsible resource management. Furthermore, a comprehensive understanding of the interplay between technological advancement, operational efficiency, and environmental impact will be paramount in shaping the future of these essential facilities. Research and development in sustainable processing techniques and resource conservation hold significant potential for enhancing the long-term viability and impact of processing operations in various sectors.
Article Recommendations
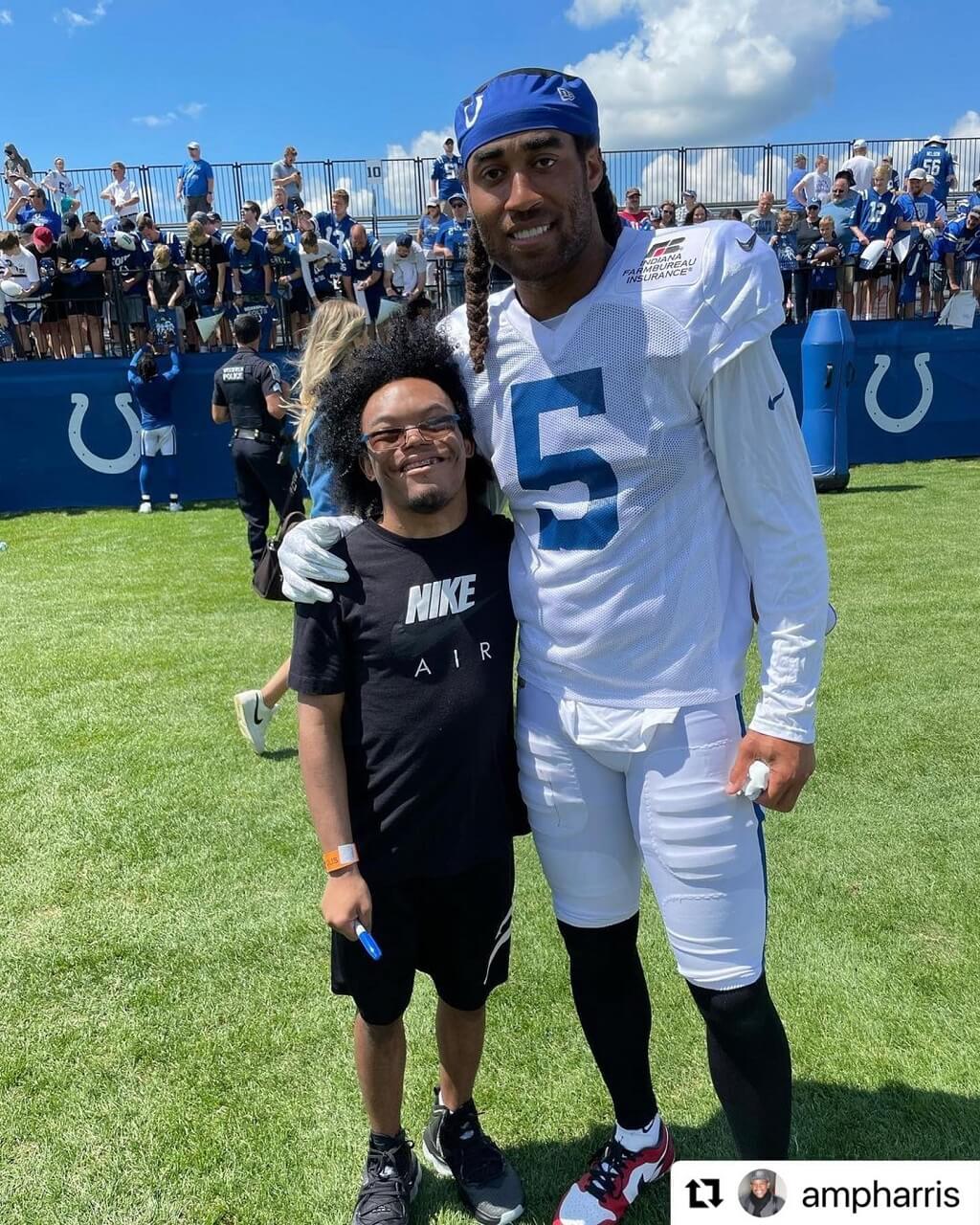
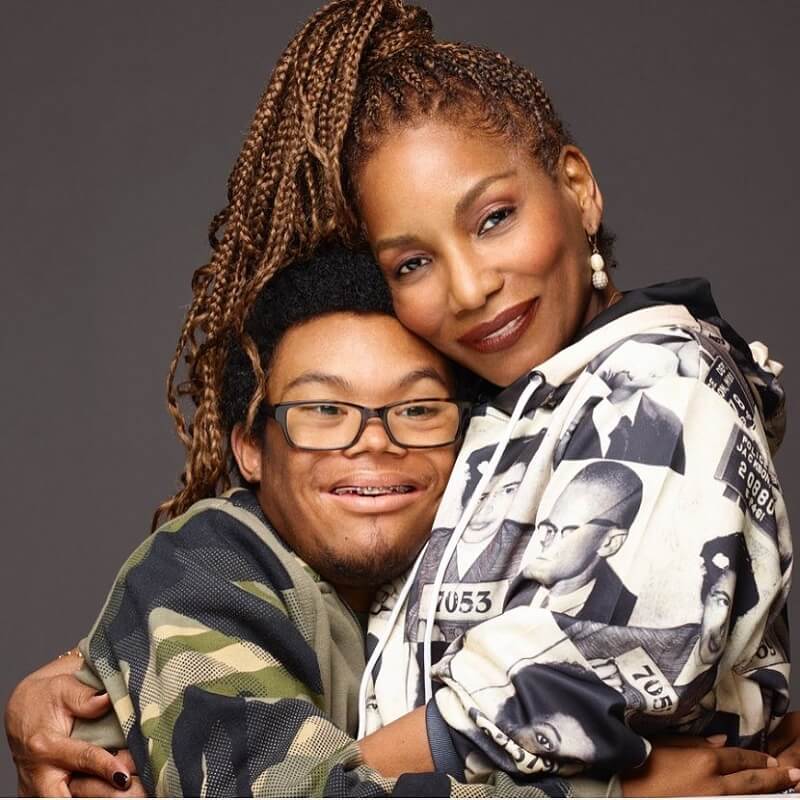
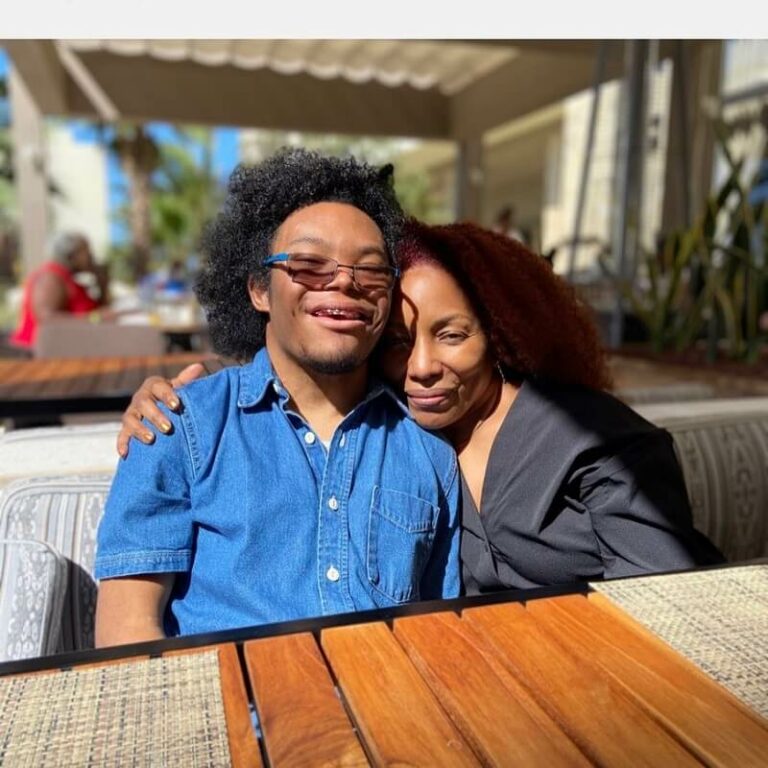
ncG1vNJzZmibkafBprjMmqmknaSeu6h6zqueaJmTqb%2Bmv9KeqmavmKR6pbHFoqWenF%2BbrrOtw2akoqScqHupwMyl