What distinguishes this specific type of concrete, and why is it significant?
This particular grade of concrete, often denoted by its strength characteristics, is a standardized construction material. It possesses a specific mix of cement, aggregates (like sand and gravel), and water, resulting in a predetermined compressive strength. This strength is crucial in structural engineering, and its precise specifications are part of engineering standards and regulations. For instance, in structural applications, a specific compressive strength is needed to withstand the loads imposed on a building or infrastructure element.
This concrete grade's importance lies in its standardized performance. Its specified strength allows for dependable calculations and design in projects where structural integrity is paramount. This predictability in performance is vital for engineers and contractors, ensuring safety and reliability in construction. The precise mixture and manufacturing protocols underpin its consistent characteristics. Over time, the production standards have evolved to include quality control measures. These practices are key to the quality and safety of the finished structure.
Further exploration into this type of concrete would include examining its application in various construction projects, comparing it to other concrete grades, and detailing its manufacturing process. Understanding the nuances of its mix design, curing processes, and performance under different environmental conditions can offer deeper insights.
no12 concrete
Understanding the specifics of no12 concrete is vital for construction projects demanding a particular compressive strength. Its precise composition and properties are critical for structural integrity and safety.
- Compressive strength
- Mix design
- Material specifications
- Curing protocols
- Quality control
- Durability standards
- Structural applications
- Regulatory compliance
The key aspects of no12 concrete, a specific grade, highlight the importance of precise control throughout production. Compressive strength, dictated by the mix design and materials, is crucial for structural applications. Meeting material specifications, adherence to curing protocols, and robust quality control measures are essential for predictable and durable outcomes. Thorough understanding of no12 concrete's suitability for particular structures, alongside regulatory compliance, leads to safe and lasting construction. For example, a bridge's foundation demanding no12 concrete ensures its capacity to bear heavy loads. Ultimately, these aspects contribute to the longevity and safety of engineered structures.
1. Compressive Strength
Compressive strength is a fundamental property of no12 concrete, directly influencing its structural capacity. This measure of resistance to crushing forces is critical in determining the suitability of the material for various applications. Understanding the relationship between compressive strength and no12 concrete is essential for ensuring the integrity and safety of structures.
- Definition and Measurement
Compressive strength represents the maximum pressure a material can withstand before permanent deformation or fracture when subjected to a crushing force. It is typically measured in megapascals (MPa) and rigorously tested according to established standards. This standardized testing ensures consistency in assessing no12 concrete's capacity to resist loads in various structural applications.
- Influence on Structural Design
The compressive strength of no12 concrete dictates the permissible loads a structure can safely bear. Engineers utilize this value during the design phase to calculate suitable dimensions and reinforcement requirements, ensuring the structure's stability and longevity. Lower compressive strength values require more material or reinforcement to achieve the desired structural capacity.
- Impact on Application Suitability
No12 concrete, with its defined compressive strength, dictates its suitability for specific construction tasks. Applications requiring significant load-bearing capacity, such as foundations or load-bearing walls, necessitate higher compressive strengths. Conversely, less demanding applications may utilize lower strength concrete, promoting economic considerations in construction.
- Role in Quality Control
Ensuring consistent compressive strength is a core aspect of quality control during no12 concrete production. Standardized testing procedures and adherence to prescribed mix designs guarantee that the concrete meets the necessary strength requirements. This control minimizes the risk of structural failure and ensures the reliable performance of the constructed elements.
In summary, compressive strength is not merely a numerical value for no12 concrete but a critical determinant of its structural performance. Accurate calculation, consistent testing, and application-specific consideration of compressive strength are vital for safe and durable structures utilizing this material.
2. Mix Design
Mix design is fundamental to achieving the desired properties of no12 concrete. The careful selection and proportioning of constituent materialscement, aggregates, water, and potentially admixturesdirectly influence the concrete's final compressive strength, workability, durability, and other essential characteristics. Optimizing this mix is crucial for ensuring no12 concrete meets the predetermined standards necessary for its intended structural applications.
- Component Selection and Quantification
Precise quantities of each material are critical. Variations in the type and grading of aggregates, for instance, can significantly affect the concrete's strength and durability. Cement type and content directly impact the concrete's early-age strength development and long-term durability. Water content is equally crucial, influencing workability and ultimately the concrete's final strength and consistency. The careful selection and precise quantification of these components are essential for consistently achieving the desired compressive strength for no12 concrete.
- Workability and Placement Considerations
The mix design must consider how easily the concrete can be placed and compacted in the formwork. Too-high water content reduces strength, while excessively low water content hinders placement. Appropriate admixtures can significantly impact workability without compromising strength. Careful consideration of these factors allows for efficient placement and ensures the no12 concrete fills the formwork correctly and avoids voids. This consideration is crucial for maintaining the desired structural integrity.
- Strength and Durability Requirements
Mix design directly correlates to the concrete's long-term durability and performance under load. For no12 concrete, the mix must consistently achieve the required compressive strength and address potential factors like freeze-thaw cycles and chloride ingress. Considerations like aggregate size, shape, and surface texture, combined with the optimal cement content, directly influence the no12 concrete's durability in various environmental conditions. This attention to detail ensures the structure's long-term viability and safety.
- Cost-Effectiveness
Mix design must consider the economic aspects of material selection. Optimizing the mix ensures the desired strength and properties are achieved at the lowest possible cost. Finding the balance between strength, workability, durability, and cost-effectiveness is a key aspect of responsible and efficient concrete production for no12 concrete applications. Minimizing material usage while maintaining quality is crucial for the financial feasibility of construction projects using this specific grade.
In conclusion, the proper mix design for no12 concrete is not simply a matter of combining ingredients. It requires a comprehensive understanding of the material properties, the structural application, the environmental conditions, and the economic constraints. This comprehensive approach ensures the production of no12 concrete with consistent strength, durability, and cost-effectiveness, guaranteeing the safety and longevity of the resulting structure.
3. Material Specifications
Material specifications are intrinsically linked to the quality and performance of no12 concrete. These specifications define the precise characteristics of the constituent materials cement, aggregates (sand and gravel), water, and potential admixtures required for the production of this specific grade. Adherence to these specifications is paramount for achieving the desired compressive strength, durability, and workability. Deviation from these standards compromises the structural integrity and longevity of the resultant concrete structure, potentially leading to costly repairs or structural failures.
The specifications for no12 concrete dictate the type and grading of aggregates, ensuring appropriate particle size distribution and overall mix consistency. Variations in aggregate quality directly impact the concrete's ability to resist compression and shear forces. Similarly, precise cement type and content are crucial for controlling the concrete's early-age strength development and long-term durability. Variations in cement quality can negatively affect the setting time and the overall strength of the concrete. Water content, while seemingly simple, critically influences workability and ultimately the concrete's compressive strength. Excessive water leads to reduced strength and potential segregation. Conversely, insufficient water impairs workability, hindering proper placement and potentially leading to voids within the structure. Finally, admixtures, if specified, are carefully regulated to achieve specific enhancements to the concrete's properties, such as increased workability, increased durability, or enhanced early-age strength. Deviation from these specifications can diminish the effectiveness of admixtures, leading to reduced expected benefits. Compliance with material specifications ensures consistency and quality control throughout the production process. Examples include bridges and high-rise building foundations, where the structural integrity depends directly on the precise composition of the concrete.
In essence, material specifications for no12 concrete are not merely guidelines; they are fundamental prerequisites for producing a reliable and durable construction material. Understanding the interrelationship between these specifications, the characteristics of no12 concrete, and the design of structures built with this material is crucial for ensuring safety, longevity, and cost-effectiveness in construction projects. A thorough understanding of material specifications empowers engineers and contractors to make informed decisions, mitigate risks, and maintain consistent quality, thereby contributing to the overall success and durability of the constructed projects. Failure to meticulously adhere to these standards can lead to structural deficiencies, safety concerns, and potentially substantial financial losses.
4. Curing Protocols
Curing protocols play a critical role in the development and long-term performance of no12 concrete. These protocols detail the procedures necessary to maintain the proper moisture content and temperature of freshly placed concrete. Proper curing ensures hydration of cement, a vital chemical reaction that ultimately determines the concrete's strength and durability. Failure to adhere to appropriate curing protocols can significantly compromise the concrete's compressive strength and long-term durability, leading to potential structural issues. The specific protocols for no12 concrete must consider environmental factors like temperature and humidity to maintain optimal conditions for hydration.
The effectiveness of curing is directly linked to the concrete's ability to develop its designed strength. Adequate moisture content during the early stages of curing fosters the hydration process, essential for the formation of strong chemical bonds between cement and aggregates. Maintaining a consistent temperature range also supports this process. Variations in temperature can impede hydration, leading to weak concrete and reduced structural integrity. Appropriate curing methods for no12 concrete might involve covering the concrete with plastic sheeting, applying water sprays, or using specialized curing compounds, all tailored to the specific environmental conditions and the project's demands. For example, in regions with rapid temperature fluctuations, specialized curing techniques are essential for maintaining the necessary hydration of no12 concrete in foundation elements of a building. Conversely, in arid climates, continuous moisture management is crucial to sustain the hydration process.
In summary, curing protocols are not an optional step in no12 concrete production; they are integral to its overall performance. Properly executed curing ensures the development of the concrete's full potential strength and durability. Ignoring or inadequately implementing curing protocols can result in significant structural compromises and safety hazards. By understanding and meticulously following the prescribed protocols, engineers and construction professionals can guarantee that no12 concrete performs reliably and consistently, meeting the design criteria and ensuring the longevity of the constructed structure.
5. Quality Control
Rigorous quality control is essential for ensuring the structural integrity and longevity of no12 concrete structures. Consistent adherence to established standards is paramount. Variations in concrete quality can compromise the strength and durability of the final product, potentially leading to structural deficiencies and safety hazards. Consequently, precise quality control procedures are indispensable in projects using no12 concrete.
- Material Testing and Verification
Thorough testing of constituent materials (cement, aggregates, and water) is crucial. Analysis verifies compliance with specifications, ensuring each component meets the required quality standards. This includes rigorous testing procedures to check for defects in the raw materials. For instance, evaluating the fineness modulus of aggregates, or conducting compressive strength tests on samples of cement, ensures consistency in the quality of the material entering the no12 concrete mix. This meticulous verification helps in maintaining the standardized compressive strength target of no12 concrete. Inconsistencies in material quality have direct implications on the final structural performance, potentially leading to weaker concrete.
- Mix Design Control and Consistency
Strict adherence to the predefined mix design is paramount. This involves precise measurement and proportioning of each ingredient. Precisely controlled mixing methods guarantee the intended consistency in concrete mixture, ensuring uniform strength throughout. Automated controls, where feasible, can minimize human error in the mixing process. Maintaining consistency in the mix design is crucial for achieving a uniform compressive strength within each batch of no12 concrete, which is essential for the structural integrity of elements built using the material.
- Monitoring and Control of the Curing Process
Maintaining a consistent and controlled curing environment is critical. This includes monitoring temperature and moisture levels during the curing period. Established curing protocols, tailored to different environmental conditions, ensure optimal hydration, thereby developing the maximum possible compressive strength in the no12 concrete. Variations in curing conditions can lead to inconsistencies in the final strength and durability of the concrete. Accurate record-keeping during curing helps assess the effectiveness of the process and identify any areas requiring adjustment.
- Field Testing and Inspection
Regular field testing of the concrete in situ provides valuable data. Verification of the concrete's properties after placement, such as compressive strength, verifies compliance with design specifications and identifies any deviations. Field inspectors meticulously examine for inconsistencies in the concrete's appearance and consistency. This on-site monitoring is crucial to ensuring the no12 concrete accurately matches the design specifications. Early detection of potential problems prevents costly or dangerous structural issues later on. For example, field tests of the freshly laid no12 concrete can indicate problematic issues with the mix design or curing procedures, allowing immediate corrective action.
Implementing these quality control measures throughout the no12 concrete production process is essential. This systematic approach significantly minimizes the likelihood of variations, contributing to the long-term durability, safety, and cost-effectiveness of the resulting structures. Consistency in quality control is directly linked to the integrity of the structure built using no12 concrete, affecting its capacity to withstand expected and unexpected stresses.
6. Durability Standards
Durability standards for concrete, particularly crucial for no12 concrete, define the material's ability to withstand environmental assaults and maintain its structural integrity over time. These standards dictate the minimum acceptable performance characteristics under various conditions. For no12 concrete, this includes resistance to factors like freeze-thaw cycles, chemical attack, and sustained moisture exposure. Adherence to these standards is essential to prevent premature deterioration and ensure long-term structural soundness. These standards translate into specific requirements for material composition, curing procedures, and quality control measures to maintain specified levels of durability. Essentially, the durability standards are a set of rules that safeguard the structural longevity of the concrete element, influencing the life expectancy of any structure that incorporates no12 concrete.
The importance of adhering to durability standards for no12 concrete is evident in real-world applications. Consider a bridge foundation. If the no12 concrete used in the foundation fails to meet durability standards, its susceptibility to deterioration due to water penetration or freeze-thaw cycles could compromise the bridge's structural integrity, leading to safety risks and significant repair costs. Similarly, in a high-rise building, where no12 concrete forms load-bearing components, compliance with durability standards is crucial to maintain the building's structural stability and longevity. Meeting these standards for no12 concrete ensures the safety and reliability of infrastructure, preventing catastrophic failures and costly repairs. Such failures would have repercussions for public safety and the financial viability of projects, highlighting the critical importance of durability standards in construction and engineering practice.
In conclusion, durability standards are not merely guidelines but essential components in specifying and ensuring the long-term performance of no12 concrete. Meeting these standards safeguards against premature degradation and underscores the vital role of quality control and appropriate material selection in construction projects. Understanding the connection between no12 concrete and durability standards ensures the safety and longevity of structures, minimizing risks and maximizing the lifespan of engineered projects. This understanding is paramount in preventing costly failures, safeguarding the public, and maintaining the structural integrity of our built environment.
7. Structural Applications
The suitability of no12 concrete in various structural applications hinges on its specific compressive strength and durability characteristics. This grade's performance directly impacts the structural integrity and longevity of the built environment, necessitating careful consideration in design and implementation. Understanding the applications where no12 concrete excels provides insight into its role in diverse engineering projects.
- Foundations and Substructures
No12 concrete is frequently used in foundations and substructures due to its ability to withstand substantial compressive loads. Its predictable strength allows engineers to design stable foundations for buildings, bridges, and other structures, effectively distributing the weight of the superstructure. This application exemplifies the reliance on no12 concrete's compressive strength to prevent structural settling or failure under imposed loads.
- Load-Bearing Walls and Slabs
In structures where load-bearing walls or slabs are required, the consistent strength of no12 concrete allows for predictable and safe distribution of loads. This consistent performance supports the structural integrity of buildings, ensuring stability against vertical and lateral forces. Examples include residential buildings, industrial facilities, and commercial structures.
- Retaining Walls and Dam Construction
No12 concrete's high compressive strength makes it a suitable material for retaining walls and dam construction. These structures need to withstand significant lateral earth pressures and hydrostatic forces, which necessitate concrete with exceptional strength and durability. This application highlights no12 concrete's importance in large-scale civil engineering projects where structural stability is paramount.
- Precast Elements in Construction
Precast concrete elements, such as beams and columns, often utilize no12 concrete. Its controlled strength allows for precise design and manufacturing, enabling complex and intricate structural forms. Precast applications demonstrate the versatility of no12 concrete in modern construction practices, leading to faster construction timelines and potentially reducing construction costs.
In summary, the widespread use of no12 concrete in diverse structural applications underscores its critical role in modern construction. Its consistent compressive strength and durability are key factors in ensuring the safety, stability, and longevity of various structural elements, from foundations to load-bearing components.
8. Regulatory Compliance
Regulatory compliance is a critical component in the production and application of no12 concrete. Standards governing this material's composition, manufacturing processes, and testing procedures are established to ensure consistent quality and safety. These regulations safeguard the integrity of structures incorporating no12 concrete, ultimately preventing potential structural failures and ensuring public safety. Compliance with these regulations is mandatory and enforced to maintain consistent and reliable strength, ensuring that structures built with no12 concrete meet pre-defined performance standards. Failure to comply can lead to significant repercussions, ranging from project delays and fines to structural instability and safety hazards.
Compliance requirements often dictate the specific types and proportions of constituent materials, like cement and aggregates. Standardized testing procedures ensure that concrete batches meet the predetermined compressive strength criteria necessary for no12 concrete. These standards address factors like water-cement ratio, aggregate size, and curing protocols. Adherence to these standards is crucial for the predictable performance of no12 concrete in diverse structural applications. A well-documented quality control process, part of regulatory compliance, tracks the consistency of each batch and material, acting as a safety net to ensure structures consistently meet established strength standards. Examples include building codes and industry standards, which mandate the use of specific testing methods and the maintenance of particular records to demonstrate compliance. Non-compliance can result in legal issues and potentially, costly and unsafe structures. This ensures public safety and safeguards the investments of stakeholders in construction projects.
In summary, regulatory compliance is not an optional step in the production and implementation of no12 concrete but an integral component in ensuring safety and maintaining structural integrity. By meticulously adhering to established regulations, the quality and reliability of the material are upheld, mitigating risks and ensuring the longevity and stability of structures built with no12 concrete. The enforcement of these regulations, alongside a robust quality control system, establishes trust and confidence in the material's performance, minimizing potential financial losses and safety concerns stemming from inadequate quality standards. This comprehensive approach underscores the critical role of regulatory compliance in protecting public well-being and promoting the responsible use of no12 concrete in structural applications.
Frequently Asked Questions about No12 Concrete
This section addresses common inquiries regarding no12 concrete, aiming to provide clear and concise answers to typical concerns. Understanding these aspects is vital for informed decisions in construction projects.
Question 1: What is the compressive strength characteristic of no12 concrete?
No12 concrete denotes a specific concrete grade with a predetermined compressive strength. The exact numerical value varies depending on the specific standards and regulations being applied. This strength value is a critical parameter in structural engineering, influencing load-bearing capacity and structural design.
Question 2: What are the key components of no12 concrete mix design?
The mix design for no12 concrete comprises carefully measured proportions of cement, aggregates (sand and gravel), water, and potential admixtures. The precise quantities of each component are critical in achieving the target compressive strength and ensuring the material's durability. Variation in these components directly affects the concrete's final properties.
Question 3: How does curing impact the strength and durability of no12 concrete?
Proper curing is essential for the development of no12 concrete's strength and durability. Maintaining appropriate moisture levels and temperature during the curing process fosters the hydration of cement, which is vital to achieving the desired compressive strength. Inadequate curing can compromise the concrete's long-term performance.
Question 4: What quality control measures are used for no12 concrete?
Rigorous quality control procedures are applied throughout the production of no12 concrete. This involves testing constituent materials, controlling the mixing process, and monitoring the curing environment. These measures ensure consistency in the concrete's properties and ensure it meets the required standards for structural integrity.
Question 5: What are some common structural applications for no12 concrete?
No12 concrete's strength and durability make it suitable for various structural applications, including foundations, load-bearing walls, slabs, and retaining walls. The material's properties make it suitable for projects demanding reliable load-bearing capacity and long-term structural soundness. Understanding these applications allows for appropriate material selection in construction projects.
Understanding these frequently asked questions clarifies the key elements associated with no12 concrete, highlighting its vital role in ensuring safe, reliable, and durable constructions.
This concludes the FAQ section and transitions to the next segment focusing on the benefits of using no12 concrete in specific structural engineering applications.
Conclusion
This exploration of no12 concrete highlights its crucial role in modern construction. Key aspects, including compressive strength, mix design, curing protocols, quality control, durability standards, structural applications, and regulatory compliance, were examined. The material's standardized properties and adherence to rigorous specifications underpin its suitability for diverse structural elements. Precise mix design, coupled with controlled curing, ensures the development of the intended compressive strength and durability, characteristics essential for long-term structural integrity and safety. The analysis underscores the importance of meticulous quality control measures throughout the production process, maintaining consistent quality and performance. The regulatory framework, encompassing material specifications and testing protocols, further emphasizes the commitment to safety and structural soundness.
No12 concrete's widespread use in foundations, load-bearing elements, and other critical structures underscores its significance in modern engineering. This thorough analysis of the material's properties and applications emphasizes the need for continued adherence to quality standards to guarantee the safety and longevity of structures. The insights provided offer a comprehensive understanding, enabling informed decisions in construction projects and promoting the responsible application of no12 concrete for future infrastructure development. Sustained commitment to these principles safeguards against potential structural deficiencies and ensures the continued reliability of this essential construction material.
Article Recommendations
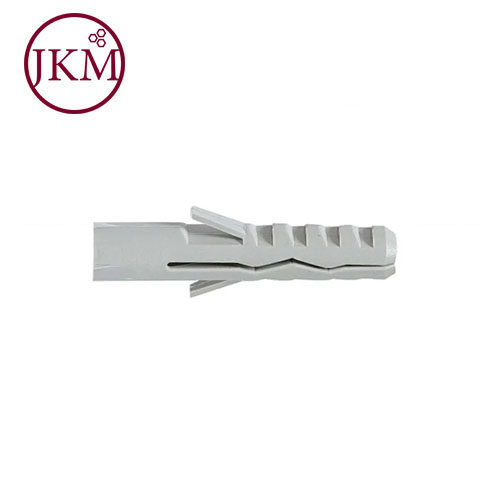

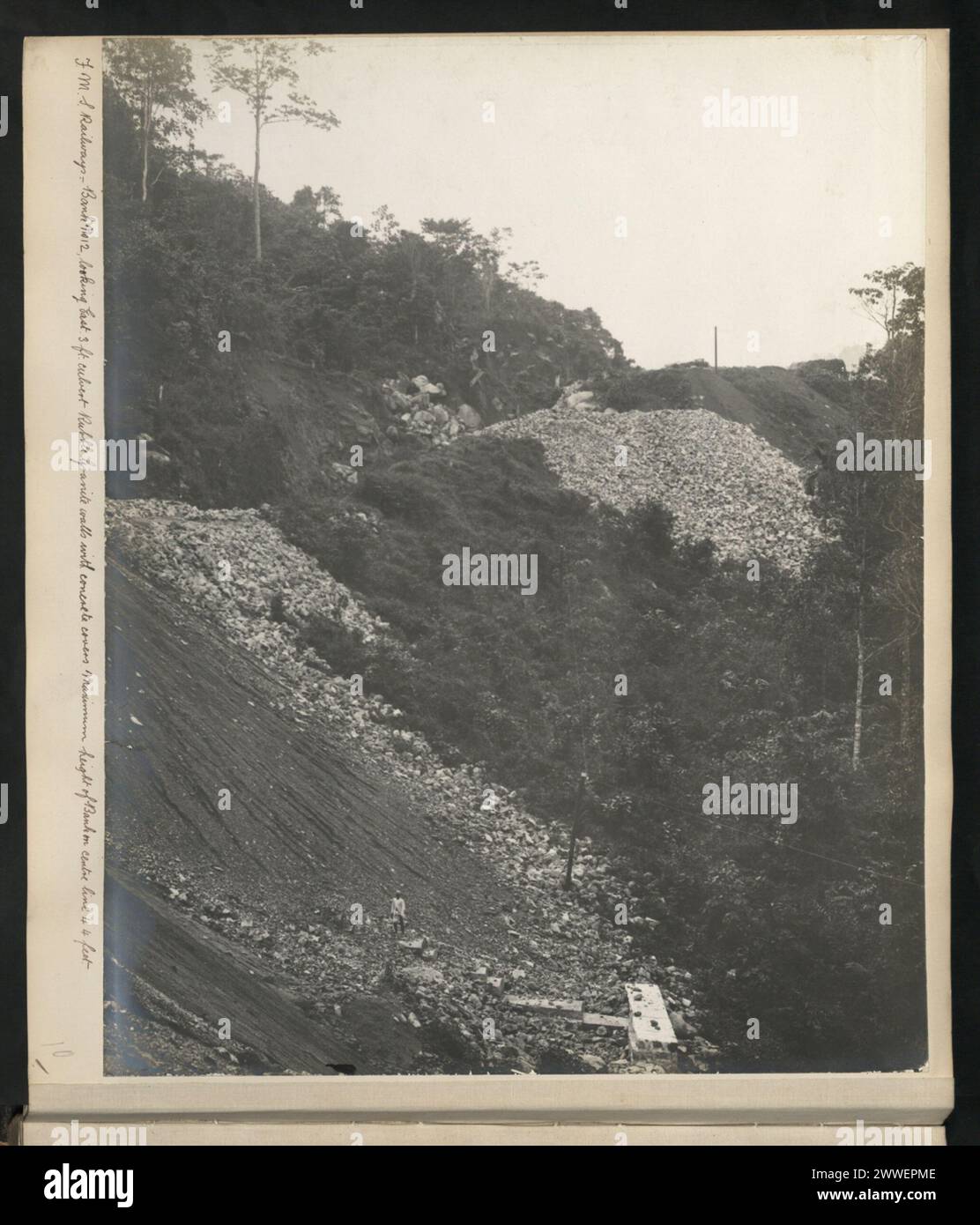
ncG1vNJzZmibkafBprjMmqmknaSeu6h6zqueaKqVmXqkrdGpnK1lnaS6prrTrGanp2FneqS7zZypnqyVY7W1ucs%3D